Global warming, rising pollution levels, extensive use of consumer electronics and natural resources, and economic and social inequality are compelling organizations to focus on driving long-term social value—not merely achieving short-term market domination. As a result, organizations are increasingly focusing on incorporating sustainability as a key pillar underpinning their business strategy, alongside innovation, technology adoption, and agile marketplace practices. Toward this end, they are embracing circular innovation best practices. The circular economy (CE) advocates the adoption of restorative or regenerative practices in business by intention and design. It fosters the use of renewable energy, eliminates the use of toxic chemicals that harm the biosphere, and reduces waste through the superior design of materials, products, systems, and business models.
One of the aims of the circular economy is to optimize resource yields by circulating products, components, and the materials in use, ensuring their highest utility at all times across both technical and biological cycles. However, organizations need to start implementing CE principles right at the product design and material sourcing stage, and throughout the entire value chain to be truly effective.
Hence, design is an integral driver in the shift to a circular economy. We cannot progress toward the circular economy without placing due emphasis on Design for Circularity (DFC). DFC is a step forward to realizing our broader vision of building a sustainable tomorrow. The practice of DFC enables engineering-centric industries including automotive, rail, aerospace, and medical technology to build more sustainable practices, products, and solutions.
The Many Merits of Traceability and the Design for Circularity Principle
Traceability is a key tool in DFC that can improve visibility into a product’s supply chain and help in verifying sustainability claims about commodities and products, thus ensuring best practices across production floors and supply chains. Due to improved product quality and raising awareness about safety in recent years, traceability has become increasingly important across automotive, electronics, aerospace, pharmaceutical, and other industries. Traceability helps organizations focus on every part of the process across the product life cycle—starting with a material’s origin, to its design into a part, to the part’s utility and use in the final product.
The supply chain for each product can be extremely complex, making traceability a legal requirement in many sectors. Traceability helps increase supply chain visibility, improves quality control systems, and reduces the risk of non-compliance to various regulatory standards.
Product traceability is not only about the manufacturer’s ability to trace a product through its distribution network to the end customer, but also their ability to retrace a product backwards through its manufacturing processing history, and farther back to the component and supplier levels.
With this feature, traceability can enable quick and prompt recall of ineffective, unsafe, or sub-standard products which may cause harm to consumers, or negatively impact the brand’s reputation and market value. Product traceability and supply chain transparency may also contribute to more efficient “end-of-use’’ practices. For example, knowing the material composition of a product can help a stakeholder decide its recyclability. The ability to view and analyze historical data from the manufacturing process allows companies to identify potentially compromised products by lot, batch, assembly, kit, revision, component, etc., limiting recalls and customer notifications to only the affected products.
Today, being green is no longer a cost of doing business. It is a catalyst for innovation, enables new market opportunities, and is a mode of sustainable wealth creation. Organizations are assessing and realigning their production processes to minimize the environmental impact of their products. The use of safe processes and green materials across their systems and value chains is helping organizations ensure the ultimate reconciliation of environmental and economic concerns by reducing the use of pollutants and hazardous substances. Green manufacturing is helping companies save costs and create sustainable development and opportunities for re-investment, all with a positive impact on the bottom line. Organizations are increasingly shifting toward responsible and accountable production practices, exploring opportunities to close the production loop and strive toward circular solutions across product value chains.
Traceability, a part of a more transparent and accountable economy, has been making inroads into a wide range of industries such as automotive, electronics, food and beverage, and pharmaceutical. For example, the meteoric rise in electric vehicle sales and car-sharing reveals growing consumer interest in sustainable mobility solutions. However, electric vehicles also pose the challenge of creating a more sustainable ecosystem associated with the production and disposal of batteries. To address this, battery manufacturers are now developing circular supply chains to ensure responsible sourcing, recycling, remanufacturing, or reuse of batteries.
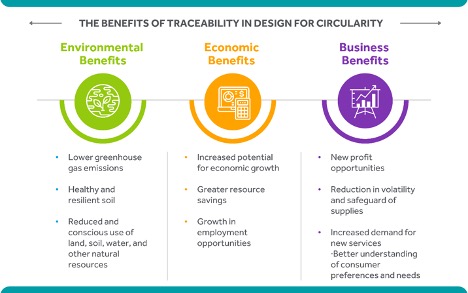